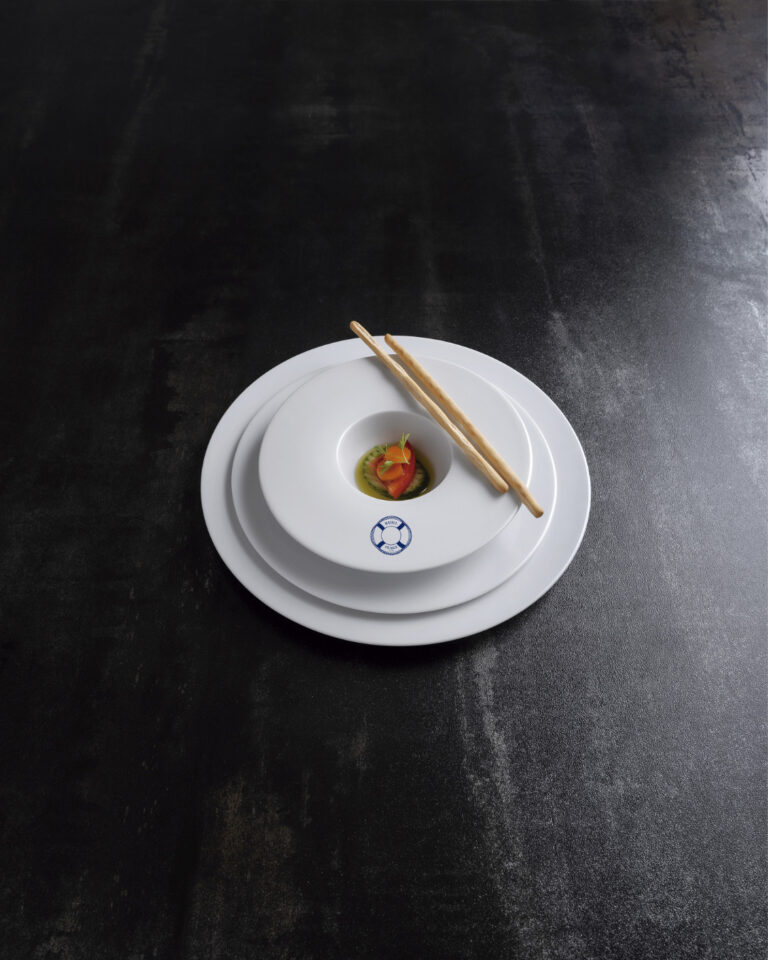
In a market characterised by the transition from mass customisation to mass personalisation (boosted by Industry 4.0), industries have to adapt to an even greater consumer participation in product design. Manufacturing processes have to be redesigned, in order to increase variety while maintaining productivity and cost. 3D printing has made it possible to begin this journey in industries where the technological barriers are not high, but across porcelain industry its adoption is still limited, despite the obvious advantages such as:
Customisation and design: complex, personalised designs, digitally conceived and produced by 3D printing porcelain, can raise the bar for creativity and creators can create unique, intricate objects that would be difficult or impossible to produce by traditional methods.
Sustainable use of materials: in 3D-porcelain printing, objects are built layer by layer, while minimising material waste. By optimising designs for material efficiency, creators can design porcelain objects, both aesthetically pleasing and ecologically efficient.
Prototyping: 3D printing allows designers to develop their projects much more quickly, efficiently and versatilely than with traditional prototyping methods. The ultimate consumer can even be part of your product’s creation.
Production on demand: 3D printing allows production to order, with objects being produced according to demand, reducing the need for large stocks and the mass production-related environmental costs.
3D printing in porcelain presents several challenges that need to be solved for widespread adoption and implementation of the technology. Some of these challenges include:
Process requirements: aspects such as high firing temperatures, shrinkage during thermal cycles and mechanical fragility mean that porcelain paste formulations for 3D printing need to be adapted without sacrificing the desired aesthetic and mechanical properties.
Printing technology: Current 3D printing technologies may not be directly applicable to porcelain. It is essential to develop specialised 3D printers, capable of printing porcelain materials with precise control of layer deposition, post-print heat treatments, among others.
Knowledge: Solving these challenges requires interdisciplinary collaboration between materials and mechanical engineers and 3D printing specialists to develop innovative solutions that solve problems that have already been solved in other industries (polymers and metals) and advance the implementation of 3D printing technology, in the porcelain industry.
Pedro Vilarinho – General Manager at HiSeedTech
Pedro Vilarinho has a degree in Electrical and Telecommunications Engineering, a master’s degree in Computer Science and a PhD in Industrial Management and Engineering. He is currently the Managing Director of HiSeedTech – a non-profit organisation that fosters the interconnection between scientific research and the market, supporting technology transfer both through open innovation and by supporting the creation of start-ups. He was a lecturer at the University of Aveiro until 2003, where he left to join the founding team of COTEC Portugal, where he remained until 2017. He holds (or has held) management positions in several start-ups, such as Exogenus Therapeutics, CEV Converde, Extremochem and Thelial Technologies.